The senior capstone design experience is an extremely important part of the materials science and engineering curriculum at Texas A&M University.
Below are descriptions of past capstone projects from Fall 2022-Spring 2023.
Projects
Project 1
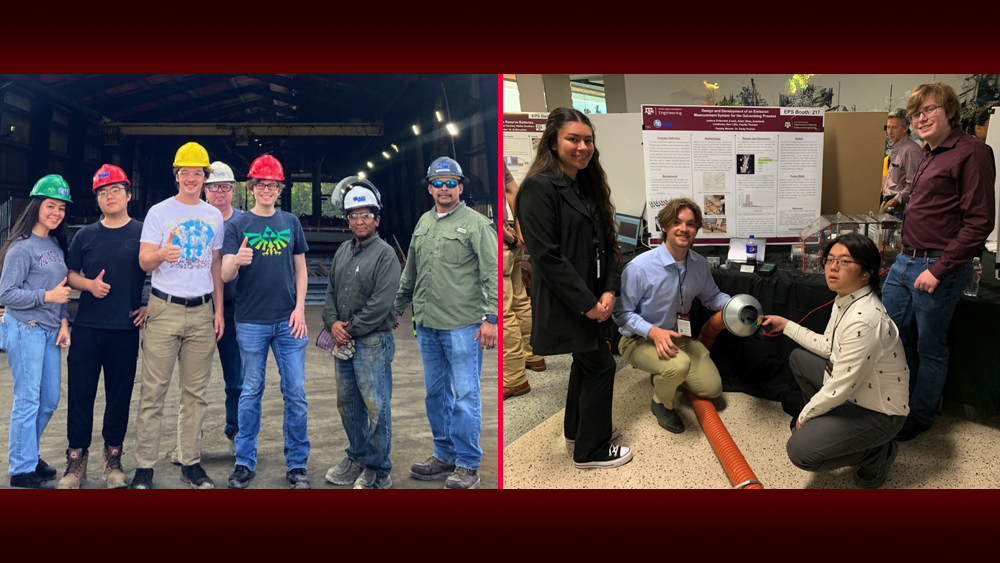
Project Name: Design and Development of an Emission Measurement System for the Galvanizing Process
Team Members: Adam Shen, Anastasia Belle Contreras, Benjamin Little, Joshua Slobodnik and Kaydia Thomas.
Synopsis: Hot-dip galvanizing is the art of coating clean, oxide-free iron or steel with a thin layer of zinc by immersion of the iron or steel article in a bath of molten zinc. Emissions released during the galvanizing process, especially generated from the burning of the flux when the article is immersed in molten zinc, is a critical environmental concern. Environmental Protection Agency (EPA) has established regulatory emission numbers that galvanizers are supposed to meet. The goal of this project is to design and fabricate an emission measurement system for a lab scale galvanizing furnace that will test the validity of EPA emission standards. The emission measurement system will be used to collect and measure different emissions released during the galvanizing process. The output of these measurements will assist in understanding and optimizing the process parameters for a more efficient galvanizing process with reduced emissions.
Project 2
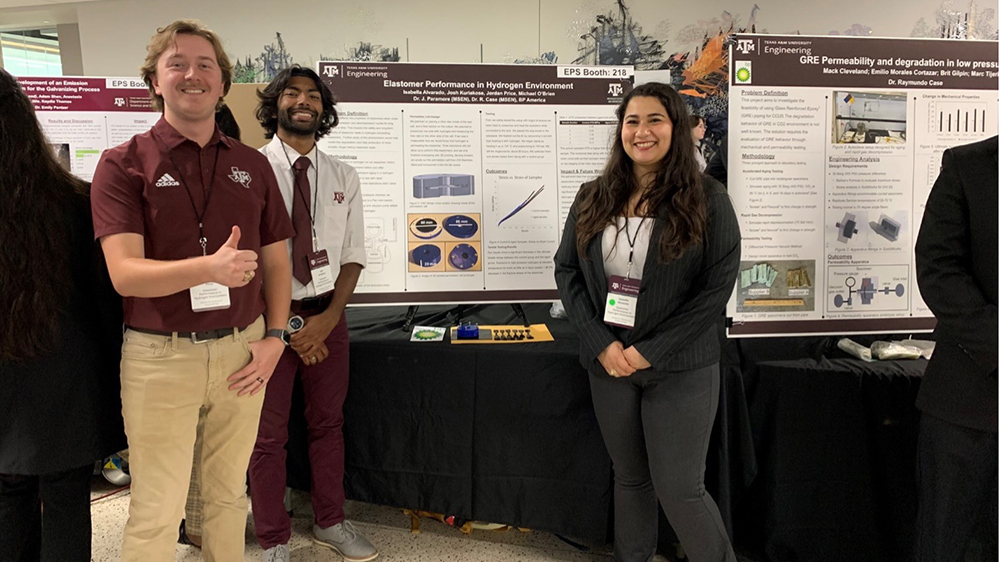
Project Name: Elastomer Behavior in Hydrogen Environment
Team Members: Isabella Alvarado, Jordan Price , Josh Kuriakose and Michael O’Brien.
Synopsis: Many polymers, when exposed to hydrogen under different conditions, may degrade in some ways, i.e. blistering and cracking upon decompression due to diffusion and dissolution of the gas in the polymer matrix. The interaction of hydrogen gas with polymer matrix and the damage resulting from rapid decompression events is a complex phenomenon which depends on multiple factors, and it is difficult to model. Among the key factors that influence the degradation risk of non-metallic components are the following: frequency and rate of depressurization, material type, seal constrain, and thermodynamics. This project aims to understand the interaction between hydrogen and elastomers for the safe operation of industrial processing facilities.
Project 3
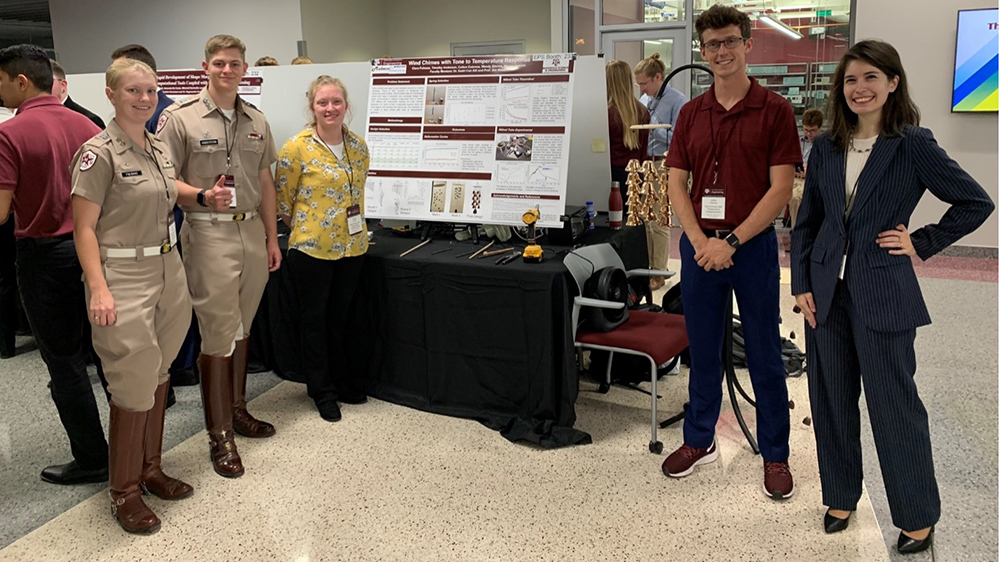
Project Name: Wind Chimes with Tone to Temperature Response
Team Members: Clara Fulsaas, Colton Colonna, Megan Nemeth, Timothy Anderson and Wendy Storms
Synopsis: Wind chimes are a popular lawn and garden accessory that add an acoustic experience to outdoor spaces. They are typically designed to produce a range of tones or a single tone when ambient winds cause tubes or bells to bump into each other or a clapper. The most popular type of wind chime consists of a set of tubes producing a set of tones surrounded by a clapper that strikes the tubes when disturbed by winds. In current designs the tubes or other ringing components are designed to produce a specific resonant frequency and tone when struck. The tone is determined by the dimensions of the tube or ringing component, the modules of the material, and the density of the material.
Components or assemblies containing active materials, such as shape memory alloys (SMA), can be designed to change the modulus or dimensions or both in response to changing ambient temperatures and thereby change the tone of a wind chime. Wind chime components built either entirely or partially from active materials, designed to change tone with temperature, would add a unique feature to this popular lawn and garden accessory and distinguish it in the marketplace. The goal of this project is to design, fabricate and demonstrate a wind chime that uses active material elements to change sound tone as a function of ambient temperature. Material selection, dimensions of the wind chime elements, and thermal response of the assembly will be investigated and a cost-effective design developed
Project 4
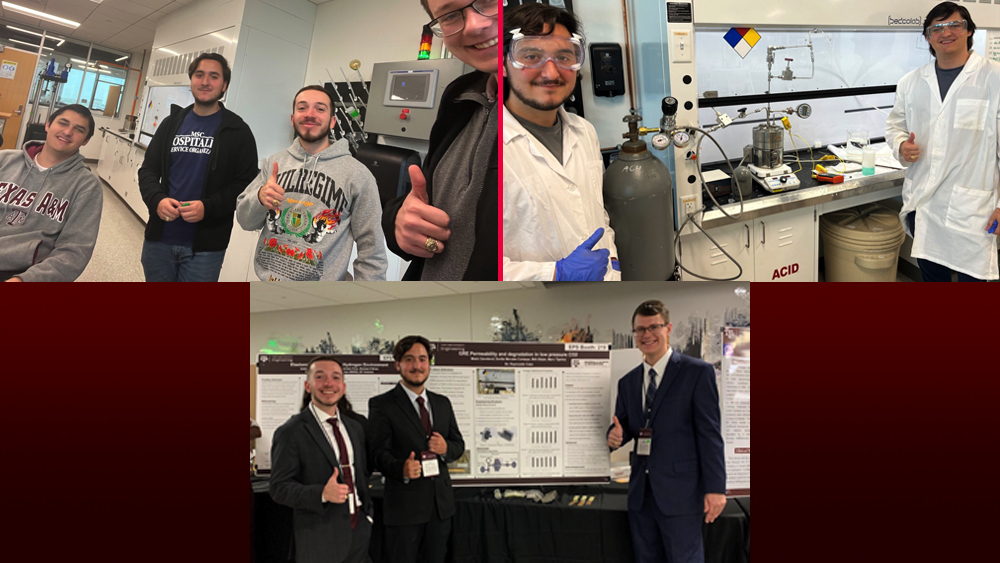
Project Name: Fiber Reinforced Polymer Permeability and Degradation in Low Pressure CO2
Team Members: Brit Gilpin, Emilio Cortazar. Mack Cleveland and Marc Tijerina.
Synopsis: Fiber-reinforced polymers (FRPs) are commonly used in structural and pressure containing components in lieu of metallic materials to reduce deterioration and prevent failures due to corrosion. They also help the environment by reducing energy during their processing and lower gas emissions to help people and the environment. However, their mechanical, chemical, and physical property limits need to be understood in more depth for specific applications where metallic components are a standard solution. For instance, FRP piping is perceived as a suitable solution for CO2 gas transport from plants to gathering systems. Understanding the operating limits of FRPs at elevated temperatures is also crucial when considering substitution of metallic materials. This project aims to understand permeation modes and degradation mechanisms of FRPs under different environmental conditions. Laboratory testing in accordance with industry standards are essential to accomplish these goals.Project 5
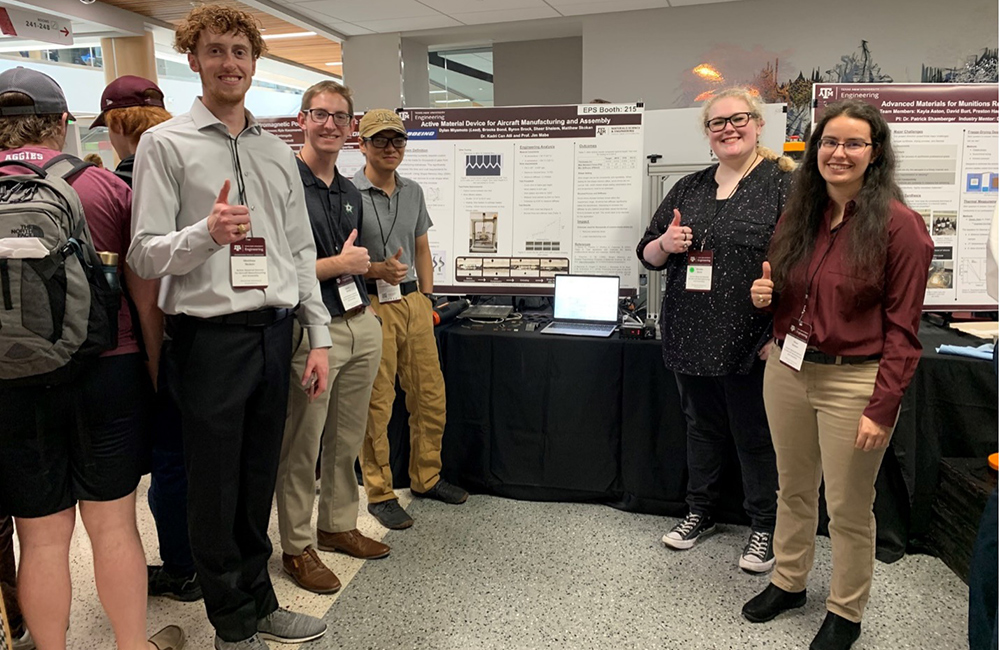
Project Name: Active Material Devices for Aircraft Manufacturing and Assembly
Team Members: Brooke Bond, Byron Brock, Dylan Miyamoto, Matthew Skokan and Sheer Shalom
Synopsis: When assembling large structures, gaps and misalignment of mating parts often occurs due to dimensional variations in the manufacturing and fabrication process. This is especially true with relatively large and flexible composite structures. Typically, custom shims are designed and manufactured to fill each gap and align mating parts. Shimming is a time consuming and costly process. One proposed solution is to use shape memory alloys (SMA) to create shim-like structures that can be inserted into a gap and when thermally activated expand to fill a wide range of gaps and align the mating surfaces. This concept could potentially eliminate the need for custom fabrication of shims for each gap or misalignment. When thermally set the ‘shims’ remains physically stiff and can structurally support the joint preventing deformation when fasteners are installed and throughout the lifetime of the part.
The goal of this project is to develop SMA devices to enable rapid alignment and assembly of large structures for cost-effective high-rate production of next-generation aerospace structures. Potential design concepts and fabrication processes will be produced, and simple proof-of-concept devices will be fabricated and tested to evaluate feasibility. Tooling and fabrication processes for a specific SMA device design, including shape set and temperature response, will be developed and fabricated. Installation methods suitable for factory assembly will be developed. Individual devices will be tested over a range of structural misalignments and assembly gaps. Thermally activated dimensional changes, loads, and installed properties will be assessed. A bench top demo will be designed and built to demonstrate an installed device supporting fastener and in-service loads.
Project 6
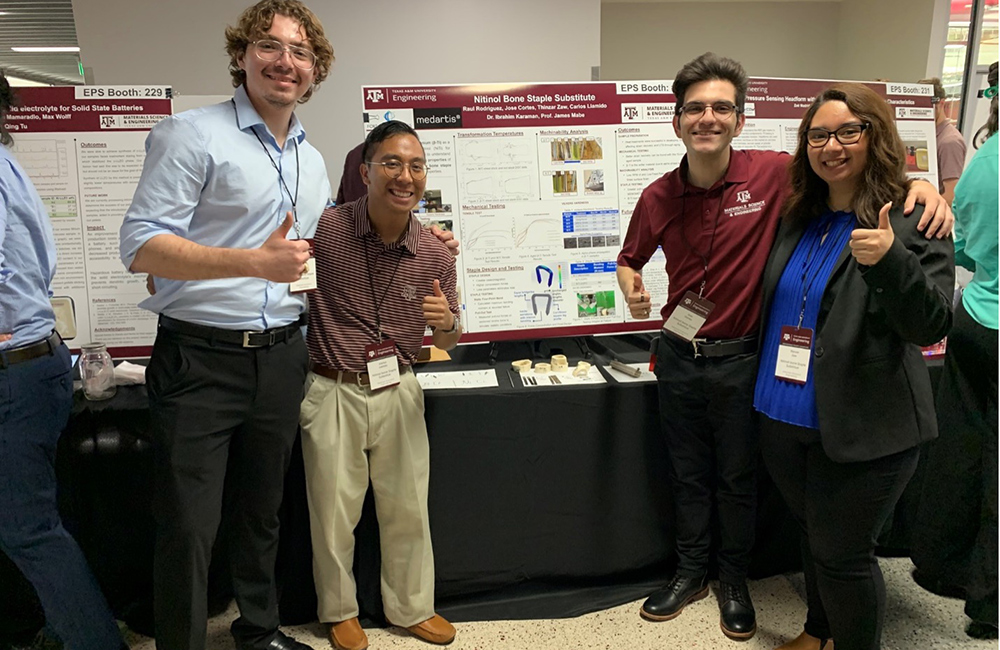
Project Name: Design of a Nickel-Free Superelastic Bone Staple with Similar Performance to Nitinol
Team Members: Carlos Llamido, Jose Cortes, Raul Rodriguez and Thinzar Zaw
Synopsis: Stabilization of bone fractures is critical to proper healing. Bone staples are a common and reliable stabilization method that reduces operating time and patient trauma when compared to a plate and screw approach. Near equiatomic NiTi, typically referred to as nitinol, is commonly used for medical devices including implanted devices that remain in the body for extended periods of time. While bone staples made from conventional materials such as steel are stiffer, nitinol bone staples are more mechanically stable fully recovering from large bending or torsional displacements and have been shown to be easier to implant. Despite nitinol’s advantages, the risk of nickel ion release after implantation and challenges in fabricating and machining nitinol parts has led medical device companies to research alternative materials for some applications. Beta titanium alloys show promise as a nickel nickel-free material with mechanical properties similar to nitinol but with better machinability. These alloys could enable improved bone staple designs, reduce cost, and eliminate the risk of nickel release into the body, and may further provide enhanced tissue-implant compatibility. The goal of this project is to measure the properties of proposed beta-Ti alloys, develop and test improved bone staple designs, and compare them to designs made from nitinol.Project 7
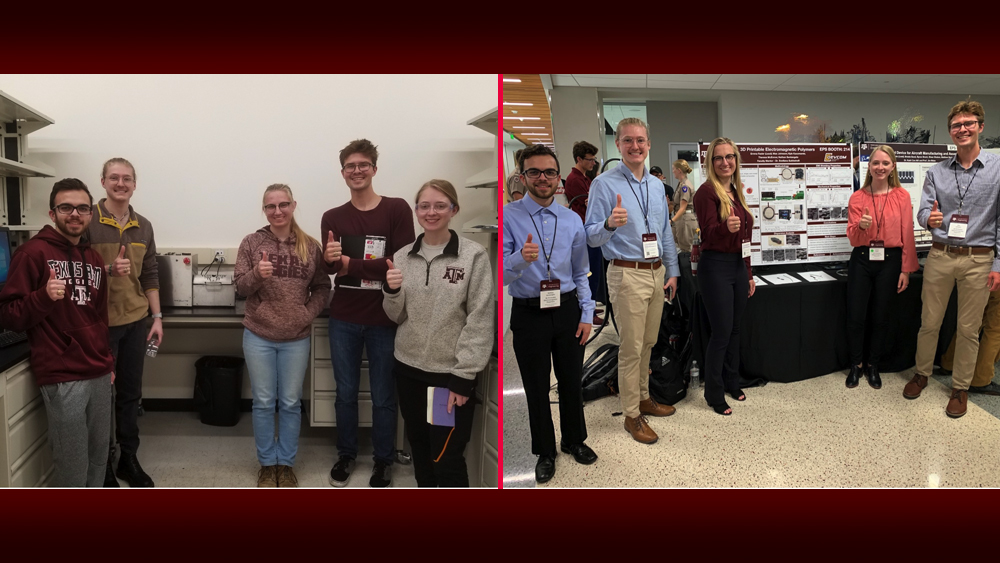
Project Name: 3D Printable Electromagnetic Polymers
Team Members:Emma Rader, Kyle Kaczmarek, Max Johnson, Nathan Santangelo and Theresa McEnroe
Synopsis: The U.S. Army seeks to develop materials which have enhanced microwave and RF properties for a variety of applications. Ideally, these materials should also have good mechanical properties and be capable of integration into systems which experience extreme environmental conditions. Currently available radio frequency (RF) materials are typically produced in flexible, flat panels. Additive manufacturing allows for rapid prototyping capabilities as well as the fabrication of parts with complex geometries. However, most polymer filaments for additive manufacturing are essentially transparent to microwave and RF radiation. The goal of this project is to develop a 3D-printable filament with enhanced electromagnetic (EM) properties in the microwave / RF spectrum. Materials with RF properties matching or exceeding that of conventional materials that can be made into filaments and utilized in commercial-off-the-shelf (COTS) thermoplastics-based 3D printers would be beneficial for military applications.Project 8
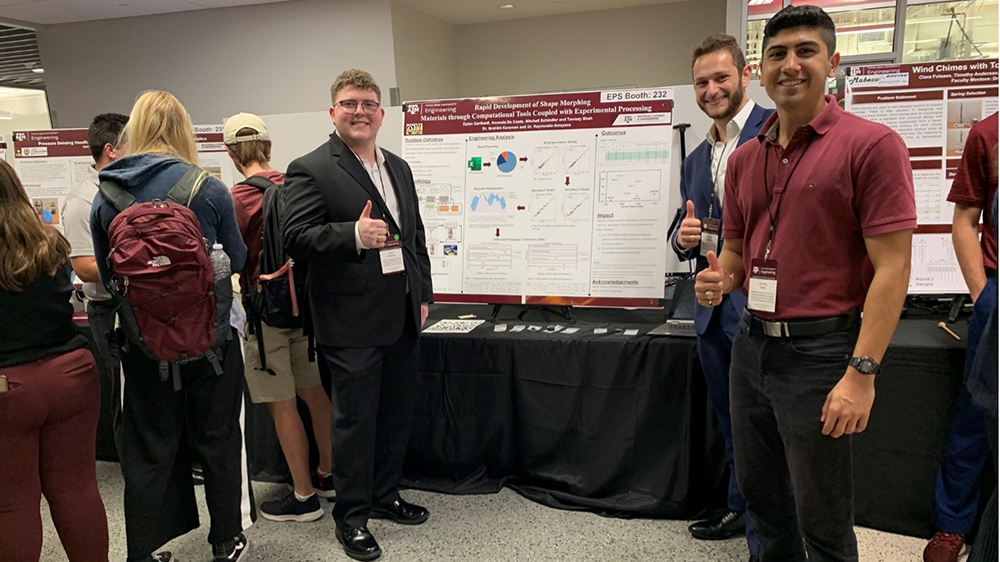
Project Name: Rapid Development of Shape Morphing Materials through Computational Tools Coupled with Experimental Processing
Team Members: Amanda De Coste, Dylan Garibaldi, Mitchell Schindler and Tanmay Shah
Synopsis: Shape morphing materials are critical for unmanned aerial systems (UAS) or projectiles which often require the ability to quickly adapt to changing flight conditions, such as air turbulence, humidity, and temperatures, which are experienced during flight, thereby improving flight characteristics such as response times, noise reduction, and improved flight performance and efficiency. The goal of this project is to rapidly identify and create commercially viable multicomponent shape memory alloys (MC-SMAs) which exhibit phase stability at elevated temperatures for use in shape morphing aerospace applications.
As a first step, an array for computational tools will be used to identify promising compositions and processing routes. These tools include using a newly developed NASA tool (https://shapememory.grc.nasa.gov/), machine learning techniques, and computational software packages such as Thermocalc’s CALPHAD software, for identifying promising MC-SMAs. As a second step, small-scale samples will be produced by implementing novel combinatorial thin film and friction stir processing approaches to generate quasi-ternary and quasi-quaternary composition-structure-function maps on MC-SMA systems which include NiTi-based SMAs with rare earths. Once these composition-structure-function maps are created, compositional spaces with promising properties, such as high transformation temperatures, low thermal hysteresis, and good oxidation-resistance, for many multicomponent compositions will be identifiable. As a third step, bulk samples based on results from the small-scale approaches will be created and their processability, thermal stability, and commercial viability will be determined by examining the phases present, thermo-mechanical properties, and processability.Project 9
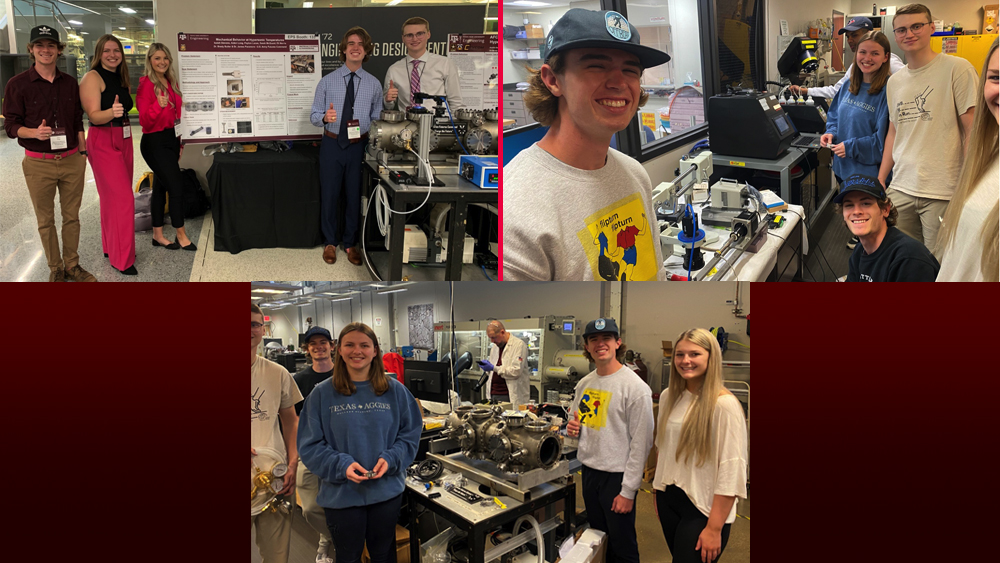
Project Name: Mechanical Behavior at Hypersonic-Relevant Temperatures
Team Members: Aiden Long (lead) Eli Norris, Isaiah Stevens, Payton Lucas and Sarah McQuaid
Synopsis: The development of new materials for use in hypersonic flight requires extensive design, development, and testing for high temperature environments. However, the current state of the art requires full-scale tensile specimens in specialized high temperature test frames, which are labor intensive and require significant quantities of material. Miniaturized testing can reduce material requirements significantly, but care must be taken to achieve reproducible and representative results especially when testing at non-ambient temperatures.
The goal of this project is to design, model, and build a reliable test rig for rapidly assessing high temperature mechanical properties of materials. The design team will outline specific actuation and heating methods to conduct tensile tests at elevated temperatures (up to 1500 °C). Tests are required to monitor load, strain, and temperature accurately and throughout the duration of the test. An additional emphasis should be placed on automating sample loading, data acquisition, and analysis during testing to allow for efficient and early testing of materials in high temperature environments.
Project 10
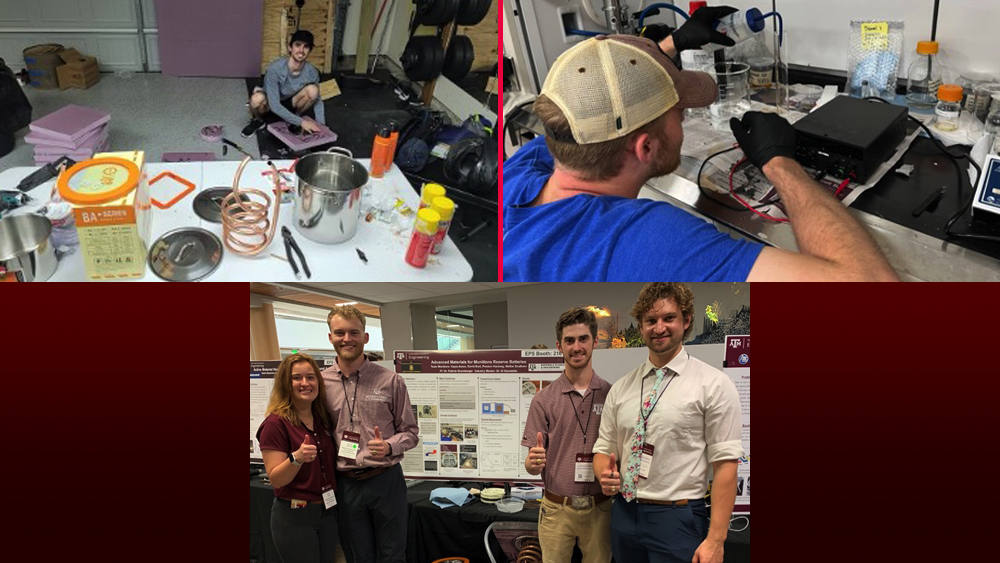
Project Name: Advanced Insulative Materials for Munitions Reserve Batteries
Team Members: David Burt, Kayla Aston, Preston Hackney and Walker Southern
Synopsis: Reserve batteries are a type of battery that provides no power until activated. They have no commercial use, currently, and Department of Defense (DoD) uses two main types: thermal batteries, that use heat to activate, and liquid reserve batteries that activate when applying pressure to an electrolyte reservoir. Reserve batteries (thermal batteries, liquid reserve batteries) are required power source for missiles, guided artillery, torpedoes, medium caliber ammunition, countermeasure devices, aircraft emergency systems, guided bombs, fuses (safe and arming circuits), sonobuoys, and mines (underwater and land). These batteries meet the uniquely needed requirements of long shelf life (excess of 20 years), high reliability through extreme temperatures and shock environments, enhanced safety, and high power for relatively short moments of time after activation.
Current state-of-the-art materials and electrodes cannot meet the power, energy, and volume requirements for developmental long-range precision munitions. With advanced capabilities needed on all of these munitions, there is a need for improved reserve batteries with longer run times and higher power output in smaller volumes. To achieve these performance improvements, this project aims to develop new advanced materials that offer increased energy densities and power densities that are producible in larger batch quantities.
Project 11
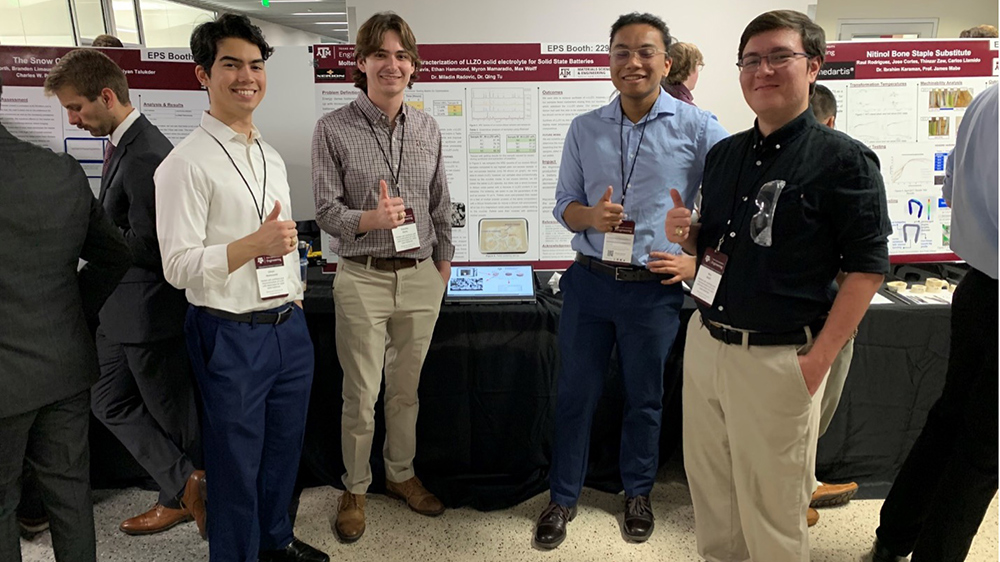
Project Name: Molten Salt Synthesis and Characterization of LLZO Solid Electrolyte for Solid-State Batteries
Team Members: Ethan Hammond, Max Wolff, Myron Mamaradlo and Timothy Davis
Synopsis: Solid-state rechargeable batteries based on Li metal anode could be a revolutionary energy storage solution, offering much higher energy density and safety compared to state-of-the-art Li-ion batteries using organic liquid electrolytes. Garnet-type LLZO (Li7La3Zr2O12) is one of the most promising ceramic electrolytes for solid-state batteries using Li metal anode. LLZO is a fast Li-ion conductor, with ionic conductivity in the range of 0.1 – 1 mS cm-1. It is mechanically strong and chemically stable against Li, both factors contributing to reversible plating/stripping of Li during battery operation. Traditional solid-state synthesis of LLZO requires high temperatures and long sintering time (>1100 ˚C, >24 h). A less energy-intensive synthesis method is therefore desired for large-scale application of LLZO in rechargeable batteries.
Recently a molten salt approach was proposed to synthesize LLZO at a lower temperature with shorter time (900 ̊C, 4 h), as compared to traditional solid-state routes. However, the molten salt method is sensitive to reaction conditions and secondary phases could form when precursor concentration and temperature are not optimal. In addition, dopant and impurities could change mechanical properties of LLZO, which may affect its effectiveness in suppressing lithium dendrite formation. Finally, electrochemical characterization of LLZO requires a thin (100-500 µm), dense film (> 90%) and good surface condition (free of contamination, surface roughness < 1 µm), which is affected by electrolyte film preparation procedures. This project aims to explore the parameter space for molten salt synthesis, with the goal of obtaining phase-pure LLZO, which will then be fabricated into electrolyte film and characterized electrochemically. If successful, this project will reduce energy consumption for LLZO synthesis and potentially lead to significant performance improvement in solid-state batteries, and will contribute to reducing their time to commercialization.
Project 12
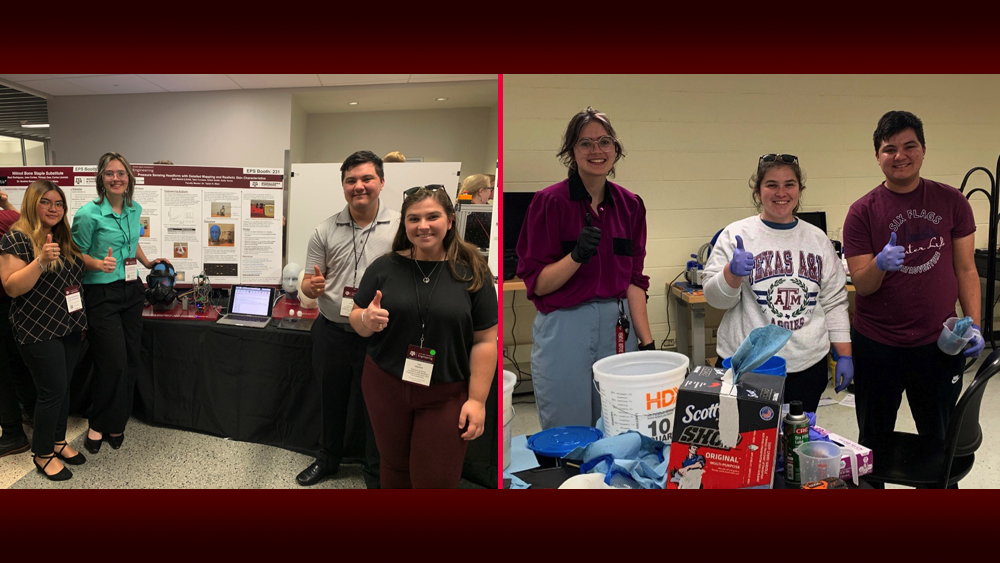
Project Name: Pressure Sensing Headform with Detailed Mapping and Realistic Skin Characteristics
Team Members: Tyler Corazao, Salem Smith, Sofia Torres and Zoë Madrid
Synopsis: US military personnel, first responders, and others who work in potentially hazardous locations are issued respirators that provide critical protection from a number of airborne threats. The protection factor (PF) of a specific respirator is the consequence of both the design of the seal as well as the fit of the equipment on the face of a given individual. While Quantitative Fit Factor (QFF) studies can be performed on the actual user community to determine specific PFs, synthetic headforms are more applicable at times during human factor studies that are often performed within the Respiratory Protection Branch. During the early development phase of next generation respirators, understanding the interface between the user and the mask is critical to the refinement of mask prototypes. However, the current state of the art headforms have two major capability gaps. First, they do not accurately mimic skin, which is a critical capability gap since mechanical and surface properties of the skin can affect the PF. Second, these headforms do not allow for recording of spatial pressure data at the critical user-respirator sealing interface. A high PF requires the entire seal to be securely pressed against the user. In order to develop more effective respirators, there is a need to specifically understand where and how the interface fails.
The goal of this project is to design and build a headform that accurately mimics the properties of the human head and has built in sensors that allow for precise spatial pressure mapping. Proper materials will be determined, and a test structure will be designed that mimics the head, with a specific focus on a surface with skin-like mechanical properties and the ability to secrete simulated sweat and other relevant exudates. The design for the headform should include an array of pressure sensors that allows for precise pressure mapping, enabling reliable and clear data generation during respiratory protection fit studies using the headform.