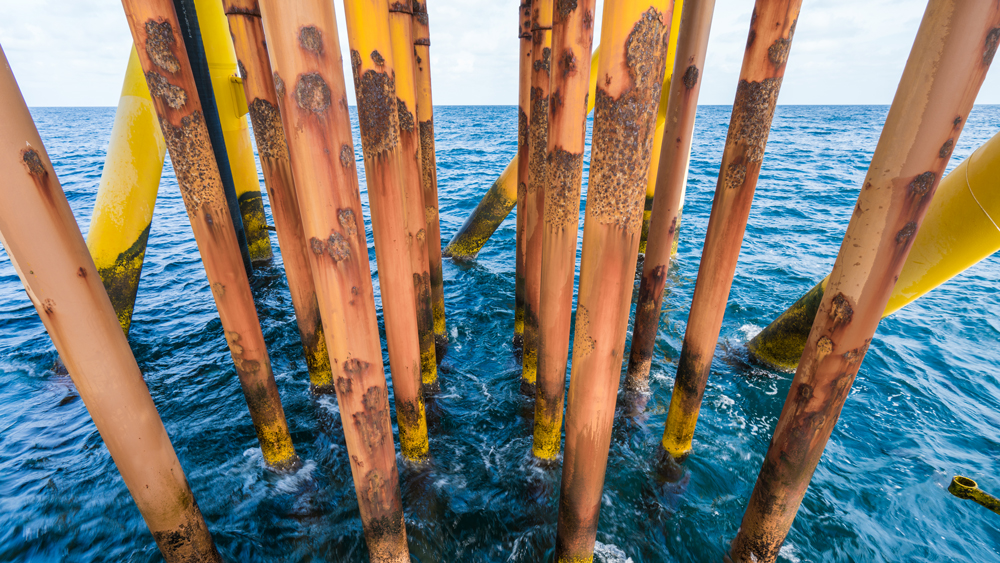
With employees' lives and a company’s costs on the line, it’s imperative for engineers to design offshore and floating structures with materials that can withstand the hazardous environment of the ocean. But there is more to keep in mind than the constant beating of the waves. Corrosion, for example, causes materials to weaken and decompose, eating away at them until they give way and deform or completely deteriorate.
And in the saline-rich waters of the sea, corrosion is an engineer’s enemy.
To help combat this, Dr. Marcelo Paredes, assistant professor in the Department of Ocean Engineering at Texas A&M University at Galveston, has been working on materials modeling – especially for engineering materials widely used by automotive, offshore and nuclear industries – and researching how corrosion affects high entropy alloys (HEAs).
“Being part of this department, which has a lot to do with corrosive environments, the corrosion resistance of metallic materials has always been a critical aspect in safety and design protocols for marine infrastructures,” Paredes said. “This study is widespread in many areas of knowledge, such as materials science, chemistry, mechanical engineering, etc., with important contributions toward its full understanding. Despite those efforts, still very little is known about corrosion-resistance properties of HEAs.”
As Paredes explained, HEAs – or alloys that are formed by mixing equal or relatively large proportions of five or more elements – offer new opportunities for applications in engineering areas due to their enhanced qualities.
“The main driving force behind these advances is the necessity to discover new materials that will be stronger and resistant, with improved mechanical and chemical characteristics for energy production and offshore installations and low-density, low-cost alloys for transportation,” he said.
In an international and multidisciplinary effort to both better understand the corrosion process and to design two distinct corrosion-resistant HEAs (FeAlNiCu-Cr and FeAlNiCu-Ti), Paredes has teamed up with researchers from the National Corrosion and Materials Reliability Lab in the Department of Materials Science and Engineering at Texas A&M University, and Dr. Pradeep Konda from the Indian Institute of Technology Madras in Chennai, India. Together, they aim to understand how corrosion influences various mechanisms of deformation at different acidity levels and loading modes.
The materials’ mechanical behavior will be analyzed at Texas A&M and the materials’ phase formation, stability and evolution will be analyzed – down to near-atomic resolutions – at the Indian Institute of Technology Madras.
“I believe that tackling this challenging problem of materials design is a very productive joint cooperation that could be established to explore the potentials of HEA as next-generation materials for engineering applications in aggressive environments,” Paredes said.