
Although extremely flammable, cotton is one of the most commonly used textiles due to its comfort and breathable nature. However, in a single step, researchers from Texas A&M University can reduce the flammability of cotton using a polyelectrolyte complex coating. The coating can be tailored for various textiles, such as clothing or upholstery, and scaled using the common pad-dry coating process, which is suitable for industrial applications. This technology can help to save property and lives on a large scale.
“Many of the materials in our day-to-day lives are flammable, and offering a solution to protect from fire benignly is difficult,” said Maya D. Montemayor, a graduate student in the Department of Chemistry at Texas A&M and the publication’s lead author. “This technology can be optimized to quickly, easily, and safely flame retard many flammable materials, offering vast protection in everyday life, saving money and lives of the general population.”
Current studies developing flame retardant coatings deposited via polyelectrolyte complexation require two or more steps, increasing the time and cost to coat a material effectively.
In contrast, this study recently published in ACS Publications hopes to achieve the same results using only one step. The researchers address this issue by incorporating a volatile base, a molecule that evaporates under ambient conditions. Using ammonia as the volatile base, the base evaporates to reduce the pH and induce complexation (a chemical reaction that forms a stable complex) on the cotton’s surface. Until now, this technique has been proposed but never used to prepare a flame-retardant treatment.
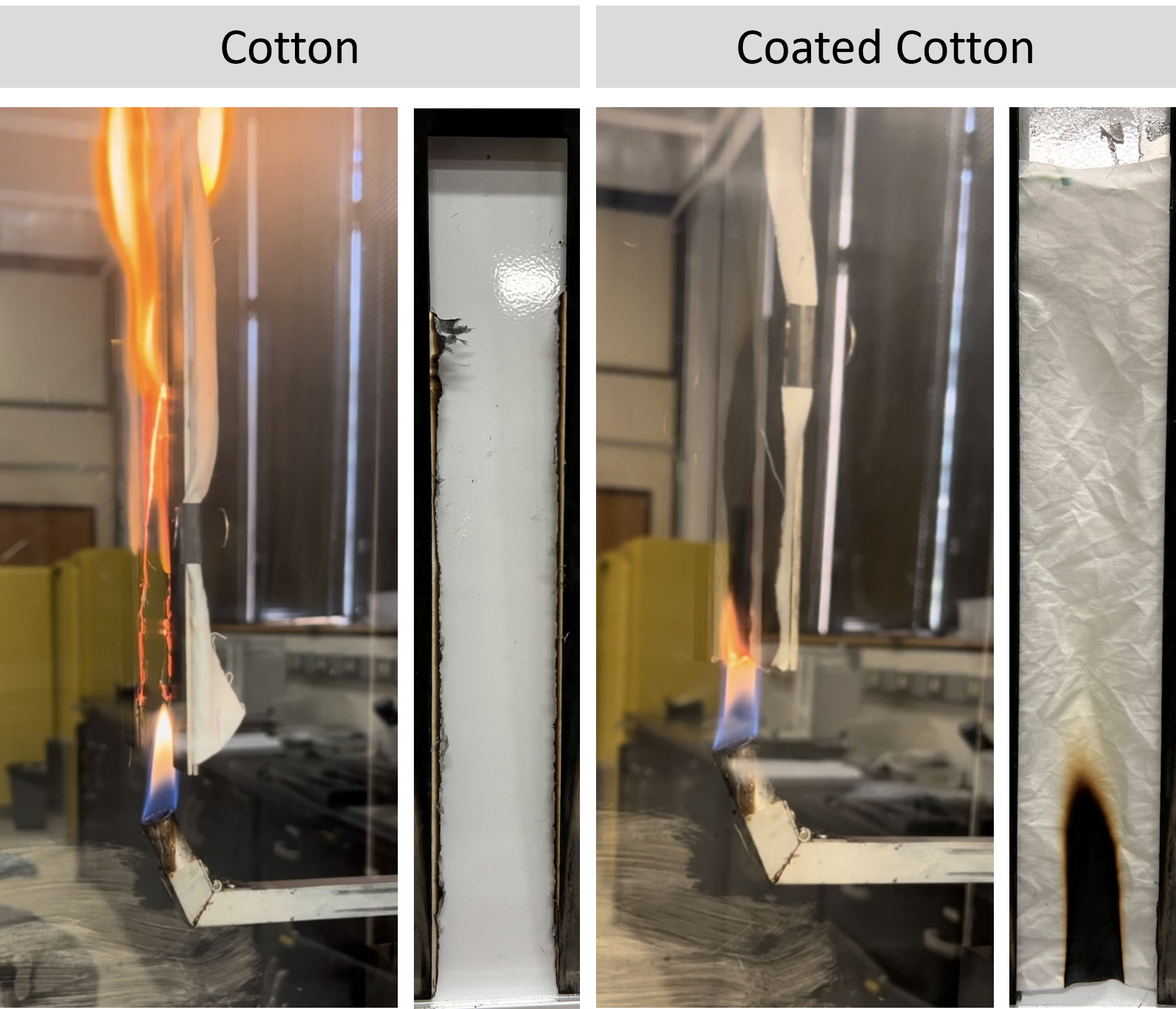
This research can be utilized to deposit polyelectrolyte-based flame-retardant coatings in a scalable and efficient manner. Other positive attributes of the technology include that it is aqueous (water-based) and non-toxic, unlike many other flame-retardant treatments.
The researchers will continue evaluating this technology in partnership with companies in hopes of using their findings to protect wood, fabric, foam and other textiles.
“This cutting-edge research offers Texas A&M recognition as one of the leaders of this technology and the opportunity for further development with external companies,” said Dr. Jaime Grunlan, Leland T. Jordan ’29 Chair Professor in the J. Mike Walker ’66 Department of Mechanical Engineering at Texas A&M. “The scope of this research positively impacts our community by improving our safety in an environmentally benign manner. TEES is licensing this and similar technologies to companies for various applications.”
Other contributors to the findings include Texas A&M graduate students Danixa Rodriguez-Melendez, Dallin L. Smith, Natalie A. Vest and Bethany Palen, and Texas A&M undergraduate students Edward Chang and Alexandra V. Moran.
Funding for this research is administered by the Texas A&M Engineering Experiment Station (TEES), the official research agency for Texas A&M Engineering.